Thread production: Methods for the production of threads
In this blog post we would like to introduce you to the different forms of thread production. Threads can, among other things:
-
-
- milled
- formed
- drilled
- rolled
- shot
- rolled and
- swirled.
-
You wonder what the difference is, which method is better?
Machining and non-cutting method
There are different methods for the production of threads. Basically, the manufacturing methods can be divided into two sub-categories: Machining and non-cutting methods for thread production. For a better understanding a short overview follows.
Machining process
In the machining process, material is removed in the form of chips. This is also the reason for the name. The machining process can be carried out manually or mechanically. The tool is given a coarser surface by the removal.
(drilling, milling, turning and whirling)
Chipless process
Therefore, no chips are removed in the non-cutting process. The required thread profile is pressed into the tool. This results in a smooth surface and a higher thread strength. In the non-cutting process, the forming process is divided into hot and cold forming.
(forming, rolling and rolling)
Let us take a closer look at the three most common methods of thread production:
-
-
-
-
-
- Drilling or cutting
- Milling
- Shapes or furrows
-
-
-
-
1. tapping and thread cutting
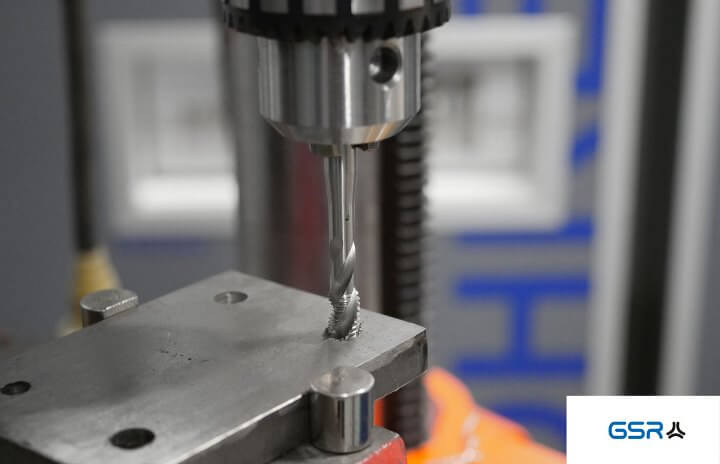
Machine tap during thread cutting
Tapping – also called thread cutting – is a cutting process. The material is removed by a step-like succession of the cutting edges.
✅ Advantages:
The field of application is very wide and the design of the tools is very simple. It can also be used for large workpieces with large diameters.
❎ Disadvantages:
With deeper threads there are problems with chip removal. There is the danger of cutting the thread.
2. thread milling
Thread milling is also a machining process. The thread milling cutter can mill an internal and external thread and can also be used on thin-walled workpieces. It is possible to produce the bore and thread in one working process. The thread milling cutter can be used on almost all materials.
✅ Advantages:
One thread milling cutter is required for different sizes. Only tools for left and right-hand threads are required. No problems with chips or tool breakage, as these can be easily removed. High cutting speed and feed.
❎ Disadvantages:
There are profile deviations with small thread profile angle and coarse pitch (e.g. trapezoidal thread).
3. Gewindeformen bzw. Gewindefurchen
Thread forming or thread grooving, on the other hand, is a chipless process. The thread profile is produced by displacing the material. The forming is carried out in a stepwise process. Due to the forming process, the thread has a higher thread strength and a better surface, as the material fibres are uninterrupted.
✅ Advantages:
No chip formation. Thread forming is suitable for greater thread depth. Longer tool life and cutting speeds. Cutting of the thread is excluded. A smoother and better surface structure is possible.
❎ Disadvantages:
Not applicable for all materials. Resharpening of the tool is not possible.
Conclusion:
Every production has its advantages and disadvantages. Which manufacturing method is preferred depends on the material, hardness and size.