These 4 factors about thread length you should know!
Connecting threads. When doing this, the connections should be designed so that the threads cannot shear and pull out in the threads (stripping the thread). The usable thread length should therefore be designed to be as long as necessary, but as short as possible to avoid unnecessary complications during creation and thus unnecessary costs. But what is the usable thread length to achieve a sufficient screw-in depth and how do you determine safe values?

Gate length for thread length
When selecting the correct threaded hole (core hole), you should consider the gate length. On the sketch, the area is marked in red. You must subtract this area from the usable thread length for a blind hole (SaLo). To be on the safe side, you should also take into account when starting the thread that the bolt does not immediately engage in the nut thread. We have marked this area in blue. The usable length should start at half of the first fully usable thread (0.5 x p).
We have thus created the conditions for achieving a sufficient screw-in depth.

Screw-in depth for threads
The actual screw-in depth for a given nominal dimension is determined by the strength class of the screw and the shear strength of the internal thread material.
Ingenieurbüro Andreas Hanke has developed a convincing set of tables according to VDI Guideline 2230, where you can easily determine the screw-in depths. We also recommend the online calculator for determining the screw-in depth from the same company. This is a very useful tool for closing the gap that the DIN standard (currently) still leaves.
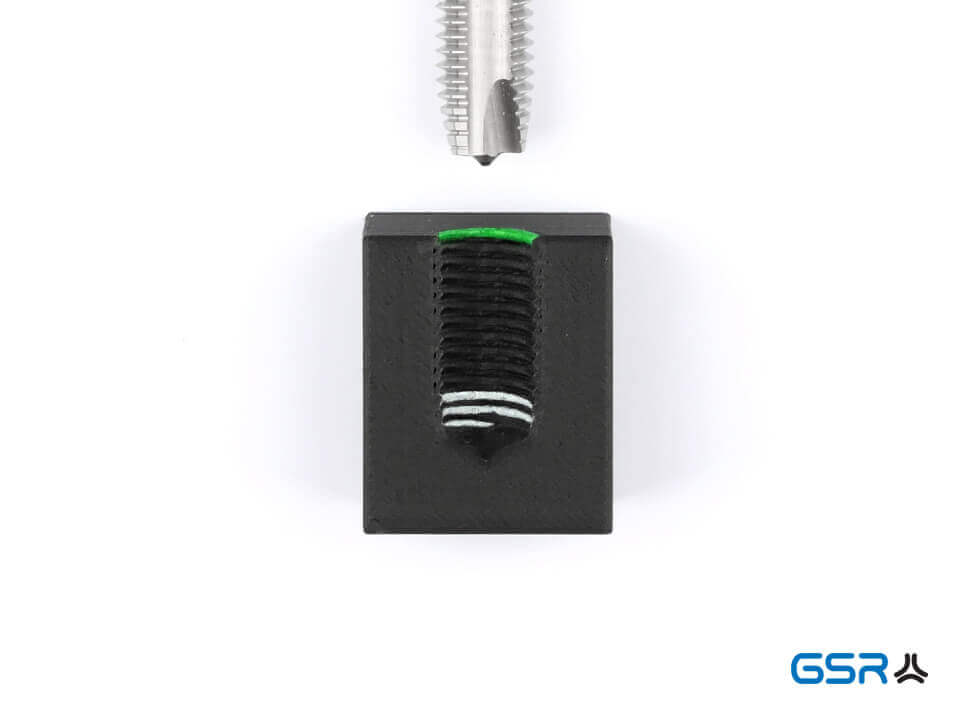
Too short and too long threads
Despite the specification of exact screw-in depths, it happens again and again in thread production that threads are too short or too long. This can have various causes. Since many threaded connections have a high safety relevance, it is necessary to provide a reliable tool in quality assurance in order to measure and control the screw-in depths with sufficient reliability. The measuring instrument manufacturer Cordt in Eschweiler offers a solution for this: The Cordicheck screw-in depth tester. The company from Eschweiler has equipped a conventional limit plug gauge with an additional scale. The zero position of the depth marker is thereby at the center of the first full thread.
Conclusion:
Safety-relevant connections require clearly defined screw-in depths. Of course, you can measure the screw-in depths with calipers and a normal plug gauge or screw. However, this is at the expense of accuracy.
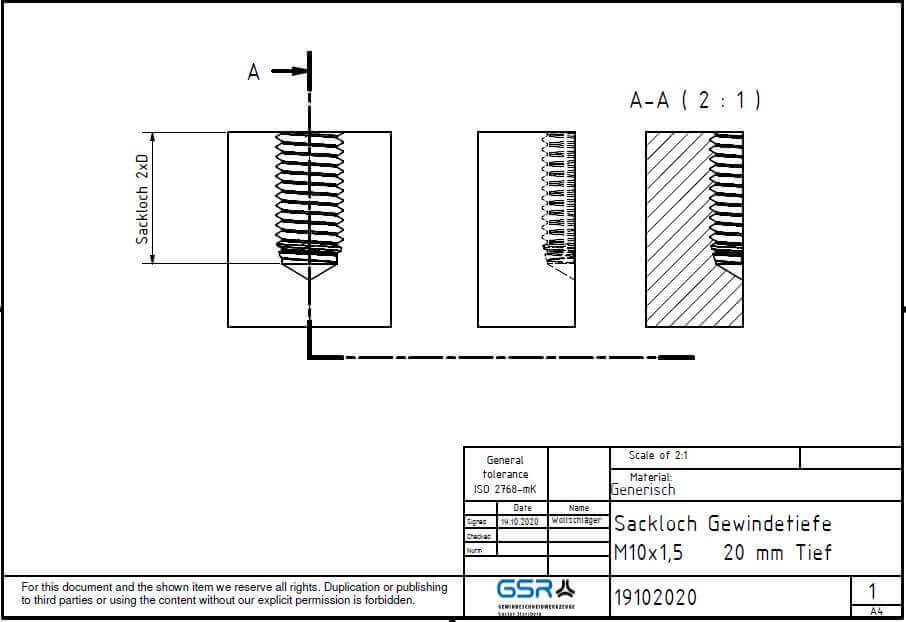
This might also be of interest to you:
- Surface coating for machine taps and twist drills
- Color ring machine tap (DIN 371 / 376)
- Avoid tool breakage with machine taps
- Extensions for machine taps
- What is a combination machine tap?
- 5 characteristics for a good tap set
Did you like the article? Do you have questions or feedback? Write to us.
By the way, you will find a large selection of taps in our store www.gewindewerkzeuge.com